BigJ
FRF Addict
- Joined
- Aug 5, 2010
- Posts
- 5,448
- Reaction score
- 1,559
The 5.4's performance numbers are well known. The 6.1 is coming and soon its numbers will be well understood too. And modifications like exhausts, intakes, power adders and tunes are here or on their way. The common dialog used to describe the differences between all of these is almost always numbers that represent "horsepower" and "torque". For a great explanation of what HP and TRQ are, see here: http://www.svtoffroad.com/showthread.php?347-Horsepower-vs.-Torque
So how are those numbers found? What tool is used to determine how well something performs? Enter, the dynamometer.... or "dyno" for short.
Generally speaking, there are two very different design of dyno's; engine and chassis. An engine dyno is designed to accept the output of an engine directly, with no transmission, gears, axles or wheels in the way. Results found on an engine dyno are what will almost always be quoted when a manufacturer throws out their numbers; these numbers do not reflect any power train loss, since the engine isn't turning anything but itself, and therefore tend to be much higher and impressive.
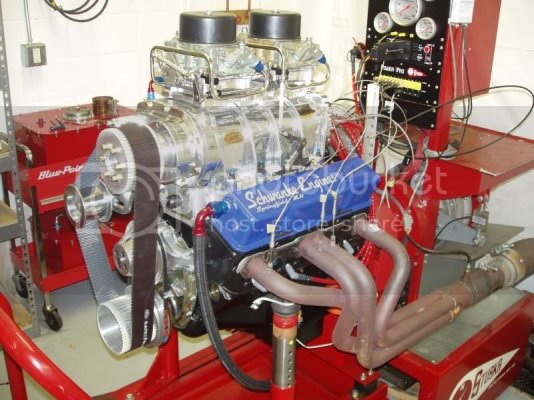
Engine dyno's are great tools for researchers and engineers. They directly and immediately show what, if any, benefit a small tweak or change has on performance. They are also often in extremely well controlled environments, and therefore consistency from run to run, day to day is almost guaranteed. An engine dyno is a great "lab tool."
But, what about those of us in the real world? What can we expect from our engines, its mods and our trucks in general, as a system... as a unit? What kind of performance can I expect when I hammer down in the salt flats?
Enter the chassis dyno.
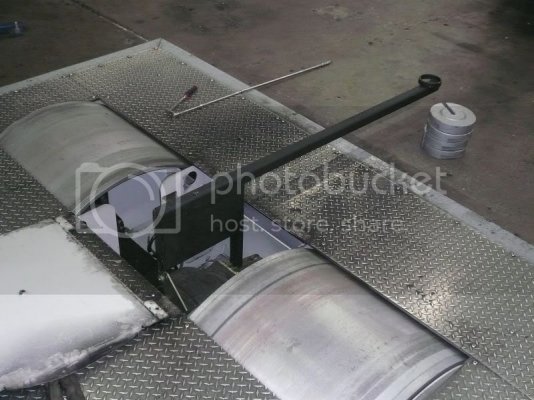
As you can see, a chassis dyno is typically made up of rollers (one for each drive wheel) in the ground or in a rack. Your truck is strapped down and the operator literally works the gas pedal, driving the wheels, and in turn spinning the rollers.
There are dozens of chassis dyno manufacturers and even more chassis dyno designs. Dynojet is perhaps the most well known, with others like Mustang and SuperFlow equally as well known and respected. They all have their uses and their advocates. They all measure values differently, and employ their own flavor of number crunching to derive results.
In its most simple form, a chassis dyno comes as either an "inertia" type or "load bearing" type. An inertia type dyno can't apply any resistance (or load) unless the vehicle is accelerating. These type of dynos are primarily used for tuning at maximum acceleration only, since they cannot be used to simulate road like conditions (hills, flat roads at steady speeds etc).
Load bearing type dynos can apply a load to its rollers. It can essentially "fight back"; the dyno can hold a vehicle at any particular throttle position and RPM. This allows a tuner to dial in and optimize the air fuel ratio and timing at that spot for that particular situation.
A dyno is capable of measuring force, or acceleration, or both. Lower cost systems will typically only measure one, and calculate the number it doesn't measure. They calculate this value based on manually input values like weight of the vehicle and tire diameter. This is less than ideal since weight can only be estimated at the time of test and this opens the door for an added variability (or sometimes, manipulation).
Of course, we could specify the same weight always; but the car may not actually weigh that weight at the time; keep in mind the general rule of 100lbs = 1/10th at the track, and you can see that its critical to get this number right each and every time you test, or your results are bound to vary.
A fully equipped system avoids this issue by measuring both force applied at the roller, as well as acceleration of the roller. Its these two values that are critical in computing power numbers; when force is multiplied by the radius of the roller, you get torque. The horsepower calculation is more complicated, but suffice it to say acceleration is a key factor. By measuring both force and acceleration, you're minimizing the variables and therefore producing more accurate results.
Depending on the capabilities of the dyno you're using, you can choose between the following four test modes:
* "simple inertia" is an inertia based mode that uses the mass of the roller to simulate load; this mode is best for acceleration testing (non adjustable load). The rollers free wheel, basically, allowing your truck to RPM out, with very little load on its way up to top speed. This is the "floor it" mode.
* "steady state control" is an inertia based mode that requires a variable load; this mode is primarily used for tuning purposes. The operator will pick various RPM speeds and hold there, and adjust the resistance of the roller to see what happens to the RPMs at various resistances. This is the "flat road" mode.
* "controlled acceleration" is a load bearing based mode that requires a variable load; this mode is primarily used for finding maximum power numbers. The rollers "fight back" against your truck, to the point where a steady speed will be maintained at full throttle (say, for example, 25mph). This is the "hill climb" mode.
* "road load" is a load bearing based mode; this mode is primarily used for simulation and diagnostic purposes. It involves a steady speed of both the rollers and engine. This is the "cruise control" mode.
In my experience, either simple inertia or controlled acceleration is the best choice for testing your own personal vehicle. I've found that controlled acceleration will typically yield more consistent results than simple inertia (+-2hp's vs +-4hp's), but simple inertia causes far less stress on the vehicle, and is more informative for seeing "up the curve" improvements. If you're interested in balls to the wall performance numbers, with the smallest impact on your truck, simple inertia is your choice.
And even despite the mode you choose or the dyno you're using, there are still dozens of factors that can affect your dyno results. Things like the weather, the gas in your tank at the time, vehicle weight (if you're not measuring both force and acceleration), power train efficiency, system heat, dyno operator, etc etc etc. Two seemingly identical trucks dyno'd back to back on the same dyno are bound to show different results. Two trucks dyno'd in different parts of the country have almost no chance of being comparable. You just can't hope to draw any useful conclusion from comparing results you found on your truck to those found on your buddy's truck in the next town over. Don't even try.
If comparing modifications, the best possible hope you have at finding useful comparisons (outside of a lab) is to replicate lab like conditions as much as possible. This means use the same truck, on the same day (same hour if possible), on the same dyno, with the same operator running it, with the same gas... change nothing except the thing you're testing, and you'll come away with useful results.
This is meant as a very basic and high level overview. The world of dynos, operators, and tuners is as diverse as the world of the automobile itself. Everyone has their way, and experience, and I'm hard pressed to say any one way is better than another. But armed with the info above, I think you should have a head start into deciding what way works best for you and your testing goals.
So how are those numbers found? What tool is used to determine how well something performs? Enter, the dynamometer.... or "dyno" for short.
Generally speaking, there are two very different design of dyno's; engine and chassis. An engine dyno is designed to accept the output of an engine directly, with no transmission, gears, axles or wheels in the way. Results found on an engine dyno are what will almost always be quoted when a manufacturer throws out their numbers; these numbers do not reflect any power train loss, since the engine isn't turning anything but itself, and therefore tend to be much higher and impressive.
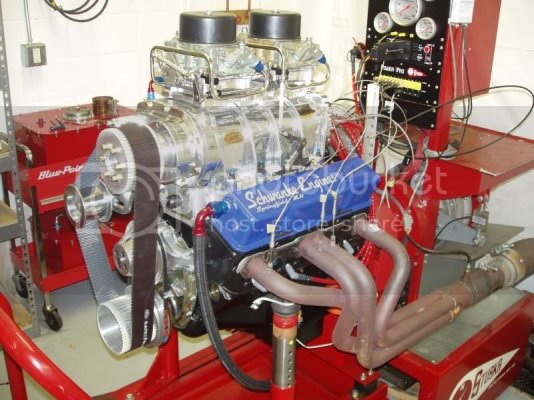
Engine dyno's are great tools for researchers and engineers. They directly and immediately show what, if any, benefit a small tweak or change has on performance. They are also often in extremely well controlled environments, and therefore consistency from run to run, day to day is almost guaranteed. An engine dyno is a great "lab tool."
But, what about those of us in the real world? What can we expect from our engines, its mods and our trucks in general, as a system... as a unit? What kind of performance can I expect when I hammer down in the salt flats?
Enter the chassis dyno.
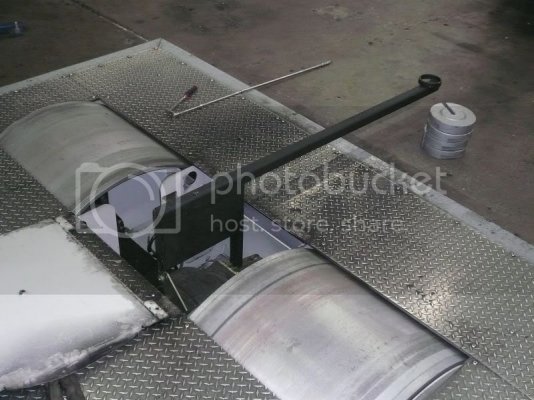


As you can see, a chassis dyno is typically made up of rollers (one for each drive wheel) in the ground or in a rack. Your truck is strapped down and the operator literally works the gas pedal, driving the wheels, and in turn spinning the rollers.
There are dozens of chassis dyno manufacturers and even more chassis dyno designs. Dynojet is perhaps the most well known, with others like Mustang and SuperFlow equally as well known and respected. They all have their uses and their advocates. They all measure values differently, and employ their own flavor of number crunching to derive results.
In its most simple form, a chassis dyno comes as either an "inertia" type or "load bearing" type. An inertia type dyno can't apply any resistance (or load) unless the vehicle is accelerating. These type of dynos are primarily used for tuning at maximum acceleration only, since they cannot be used to simulate road like conditions (hills, flat roads at steady speeds etc).
Load bearing type dynos can apply a load to its rollers. It can essentially "fight back"; the dyno can hold a vehicle at any particular throttle position and RPM. This allows a tuner to dial in and optimize the air fuel ratio and timing at that spot for that particular situation.
A dyno is capable of measuring force, or acceleration, or both. Lower cost systems will typically only measure one, and calculate the number it doesn't measure. They calculate this value based on manually input values like weight of the vehicle and tire diameter. This is less than ideal since weight can only be estimated at the time of test and this opens the door for an added variability (or sometimes, manipulation).
Of course, we could specify the same weight always; but the car may not actually weigh that weight at the time; keep in mind the general rule of 100lbs = 1/10th at the track, and you can see that its critical to get this number right each and every time you test, or your results are bound to vary.
A fully equipped system avoids this issue by measuring both force applied at the roller, as well as acceleration of the roller. Its these two values that are critical in computing power numbers; when force is multiplied by the radius of the roller, you get torque. The horsepower calculation is more complicated, but suffice it to say acceleration is a key factor. By measuring both force and acceleration, you're minimizing the variables and therefore producing more accurate results.
Depending on the capabilities of the dyno you're using, you can choose between the following four test modes:
* "simple inertia" is an inertia based mode that uses the mass of the roller to simulate load; this mode is best for acceleration testing (non adjustable load). The rollers free wheel, basically, allowing your truck to RPM out, with very little load on its way up to top speed. This is the "floor it" mode.
* "steady state control" is an inertia based mode that requires a variable load; this mode is primarily used for tuning purposes. The operator will pick various RPM speeds and hold there, and adjust the resistance of the roller to see what happens to the RPMs at various resistances. This is the "flat road" mode.
* "controlled acceleration" is a load bearing based mode that requires a variable load; this mode is primarily used for finding maximum power numbers. The rollers "fight back" against your truck, to the point where a steady speed will be maintained at full throttle (say, for example, 25mph). This is the "hill climb" mode.
* "road load" is a load bearing based mode; this mode is primarily used for simulation and diagnostic purposes. It involves a steady speed of both the rollers and engine. This is the "cruise control" mode.
In my experience, either simple inertia or controlled acceleration is the best choice for testing your own personal vehicle. I've found that controlled acceleration will typically yield more consistent results than simple inertia (+-2hp's vs +-4hp's), but simple inertia causes far less stress on the vehicle, and is more informative for seeing "up the curve" improvements. If you're interested in balls to the wall performance numbers, with the smallest impact on your truck, simple inertia is your choice.
And even despite the mode you choose or the dyno you're using, there are still dozens of factors that can affect your dyno results. Things like the weather, the gas in your tank at the time, vehicle weight (if you're not measuring both force and acceleration), power train efficiency, system heat, dyno operator, etc etc etc. Two seemingly identical trucks dyno'd back to back on the same dyno are bound to show different results. Two trucks dyno'd in different parts of the country have almost no chance of being comparable. You just can't hope to draw any useful conclusion from comparing results you found on your truck to those found on your buddy's truck in the next town over. Don't even try.
If comparing modifications, the best possible hope you have at finding useful comparisons (outside of a lab) is to replicate lab like conditions as much as possible. This means use the same truck, on the same day (same hour if possible), on the same dyno, with the same operator running it, with the same gas... change nothing except the thing you're testing, and you'll come away with useful results.
This is meant as a very basic and high level overview. The world of dynos, operators, and tuners is as diverse as the world of the automobile itself. Everyone has their way, and experience, and I'm hard pressed to say any one way is better than another. But armed with the info above, I think you should have a head start into deciding what way works best for you and your testing goals.