What Causes Stock Top Hat Failure
There are a lot of misconceptions floating around about what actually leads to stock top hats separating from the shock. The bushings are commonly pointed to as the weak link. This is far from the case. Since the shock shaft is getting pulled out of the bottom of the top hat, it is apparent that the failure is occurring at top out. The damage that people have seen where rubber is eaten away from the bushing is the result of it hitting the top hat after it has been pulled out. That is why the damage is always to the top of the bushing and concentrated on one side. Once the bushing has been pulled out, all bets are off on what might be collateral damage.
So, what causes the bushing to pull out? There is a steel core in the bushing such that it can only be pulled out if the washer is no longer retained. The two things that can cause this are damage to the top hat itself and damage to the washer. Despite that fact that what you will see here first is damage to the washer, I do not believe that is the cause because in all the instances where a top hat has failed, the washer is pretty much flat still.
Now for the fun stuff. To take the top hat to the limit, I put it in a 20 ton press and pushed down on the steel at the top of the bushing until it went bang. This is what the parts looked like after it had failed:
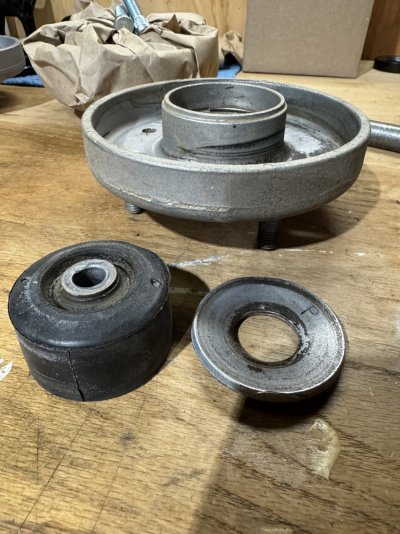
Notice the bushing is entirely fine. This bushing has about 25k miles on them including things like whoops. As you can see, the washer has been turned into a bit of a cone. It is kind of hard to see in the image, but the cone shape is not subtle at all. I have not seen a failed top hat with the washer looking like this. So, again, I don't believe the washer is the issue.
The Real Issue
Moving on to the retaining ring area. When we talk about retaining ring failure in an aluminum part, we are really talking about failure of the retaining ring groove. Before we get further, for those of you who aren't familiar, aluminum is particularly susceptible to fatigue. Unlike steel, it does not have a fatigue limit. That means eventually any aluminum part will fail. The goal in design is to make sure the number of cycles to failure is more than what the lifespan of the part needs to be. Since the retaining ring is still in the top hat, if fatigue around the retaining ring groove were to be a concern, there might be signs after taking the top hat to failure like this... and there were.
Glancing at the retaining ring ends after the explosion, a slight discoloration was noticeable to the naked eye. I suspected this might be the start of a crack, so I threw it under a microscope for a better look. This confirmed my suspicion. A small crack had initiated adjacent to the end of the retaining ring. This makes sense because there is a stress concentration at the ends of the retaining ring. Cracks will always continue to grow after they have started unless measures are taken. The growth of this crack was accelerated by the extreme force it was subjected to, however, because aluminum has no fatigue limit, it's likely this crack will always form. The name of the game if you were designing this top hat would be ensuring no catastrophic failure over the lifespan of the part.
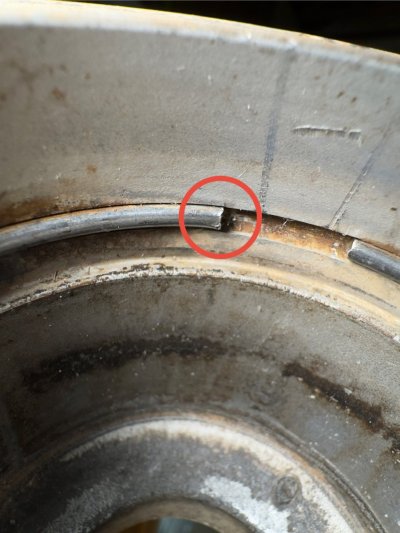
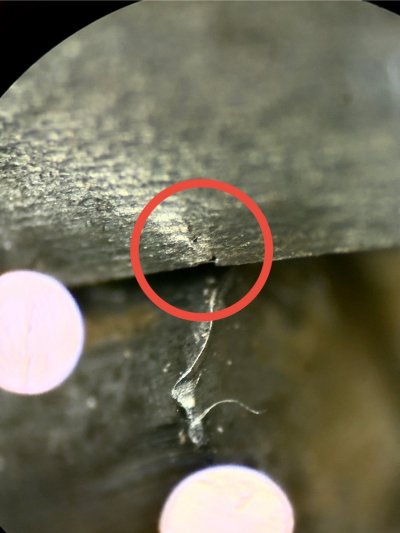
My theory, then, is that certain scenarios lead to accelerated growth of a crack at this location that ultimately results in the retaining ring/retaining ring groove no longer being able to retain the washer and, in turn, the bushing. There are two things that would primarily contribute to this: stiffer springs and heavier wheels. Since this is a failure at top out, heavier unsprung mass generates a larger top out force. The increase in top out force would be roughly proportional to the increase in unsprung mass. Stiffer springs are kind of self explanatory. The rebound tune is based on the stock springs so with stiffer springs you get higher rebound speeds. It's all pretty much like swinging a hammer. The hit is harder if the hammer is bigger and/or it's swung faster. I think the 35 and 37 trucks will largely be fine save for defects, but since the Raptor R has stiffer springs, there is a chance it's susceptible to this in its stock form.
What Can Be Done to Prevent This?
1. Stick with the stock springs and minimal preload. If you want lift, there are better ways to add it than springs. That's why I developed a set of top hats that lift 1.25" with less preload than any other lift option. The front also sees practically no weight change with weight in the bed. The Raptor has such a short bed that it's almost impossible to position weight in front of the axle. Any weight rearward of the axle actually removes weight from the front. I think a lot of people view springs as superior, but unless you need the weight capacity, they just aren't
2. Try to keep wheel weight down. That's hard to do if you don't want to run the stock tires since they are very light.
3. Run a stronger top hat.
4. Run limit straps.
There are a lot of misconceptions floating around about what actually leads to stock top hats separating from the shock. The bushings are commonly pointed to as the weak link. This is far from the case. Since the shock shaft is getting pulled out of the bottom of the top hat, it is apparent that the failure is occurring at top out. The damage that people have seen where rubber is eaten away from the bushing is the result of it hitting the top hat after it has been pulled out. That is why the damage is always to the top of the bushing and concentrated on one side. Once the bushing has been pulled out, all bets are off on what might be collateral damage.
So, what causes the bushing to pull out? There is a steel core in the bushing such that it can only be pulled out if the washer is no longer retained. The two things that can cause this are damage to the top hat itself and damage to the washer. Despite that fact that what you will see here first is damage to the washer, I do not believe that is the cause because in all the instances where a top hat has failed, the washer is pretty much flat still.
Now for the fun stuff. To take the top hat to the limit, I put it in a 20 ton press and pushed down on the steel at the top of the bushing until it went bang. This is what the parts looked like after it had failed:
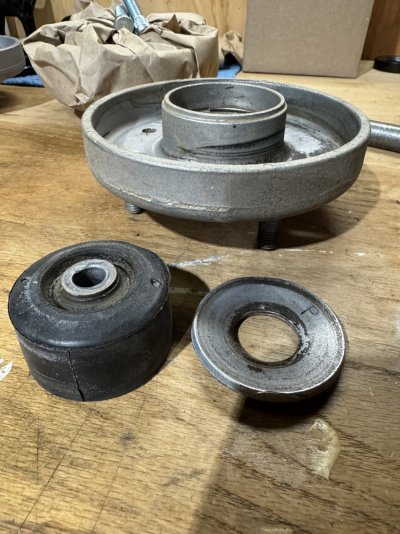
Notice the bushing is entirely fine. This bushing has about 25k miles on them including things like whoops. As you can see, the washer has been turned into a bit of a cone. It is kind of hard to see in the image, but the cone shape is not subtle at all. I have not seen a failed top hat with the washer looking like this. So, again, I don't believe the washer is the issue.
The Real Issue
Moving on to the retaining ring area. When we talk about retaining ring failure in an aluminum part, we are really talking about failure of the retaining ring groove. Before we get further, for those of you who aren't familiar, aluminum is particularly susceptible to fatigue. Unlike steel, it does not have a fatigue limit. That means eventually any aluminum part will fail. The goal in design is to make sure the number of cycles to failure is more than what the lifespan of the part needs to be. Since the retaining ring is still in the top hat, if fatigue around the retaining ring groove were to be a concern, there might be signs after taking the top hat to failure like this... and there were.
Glancing at the retaining ring ends after the explosion, a slight discoloration was noticeable to the naked eye. I suspected this might be the start of a crack, so I threw it under a microscope for a better look. This confirmed my suspicion. A small crack had initiated adjacent to the end of the retaining ring. This makes sense because there is a stress concentration at the ends of the retaining ring. Cracks will always continue to grow after they have started unless measures are taken. The growth of this crack was accelerated by the extreme force it was subjected to, however, because aluminum has no fatigue limit, it's likely this crack will always form. The name of the game if you were designing this top hat would be ensuring no catastrophic failure over the lifespan of the part.
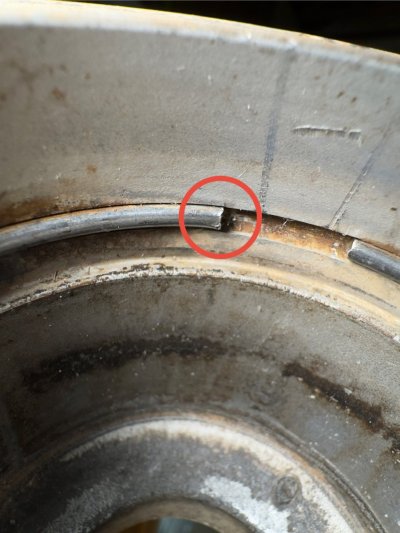
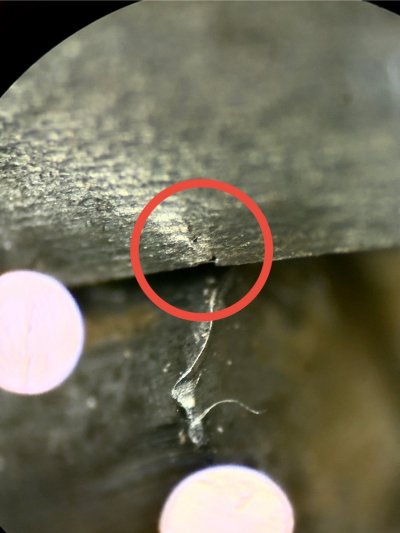
My theory, then, is that certain scenarios lead to accelerated growth of a crack at this location that ultimately results in the retaining ring/retaining ring groove no longer being able to retain the washer and, in turn, the bushing. There are two things that would primarily contribute to this: stiffer springs and heavier wheels. Since this is a failure at top out, heavier unsprung mass generates a larger top out force. The increase in top out force would be roughly proportional to the increase in unsprung mass. Stiffer springs are kind of self explanatory. The rebound tune is based on the stock springs so with stiffer springs you get higher rebound speeds. It's all pretty much like swinging a hammer. The hit is harder if the hammer is bigger and/or it's swung faster. I think the 35 and 37 trucks will largely be fine save for defects, but since the Raptor R has stiffer springs, there is a chance it's susceptible to this in its stock form.
What Can Be Done to Prevent This?
1. Stick with the stock springs and minimal preload. If you want lift, there are better ways to add it than springs. That's why I developed a set of top hats that lift 1.25" with less preload than any other lift option. The front also sees practically no weight change with weight in the bed. The Raptor has such a short bed that it's almost impossible to position weight in front of the axle. Any weight rearward of the axle actually removes weight from the front. I think a lot of people view springs as superior, but unless you need the weight capacity, they just aren't
2. Try to keep wheel weight down. That's hard to do if you don't want to run the stock tires since they are very light.
3. Run a stronger top hat.
4. Run limit straps.